FIRST Robotics - Minibot
My Senior year of high school was largely disrupted by covid. As a result my Robotics team cut its hours and there was no new competition for the season. To keep our members engaged, we worked on a demo minibot that could pick up tennis balls as a side project. For this project, I designed the intake system, including all of the CAD and prototyping.
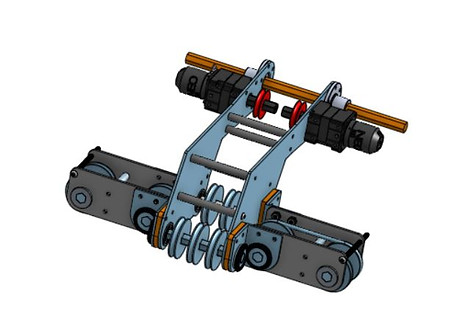
Intake V1 - Beavertail Design
The beavertail design was a known FRC design that used pullets in two directions to drag the tennis balls to the center of the mechanism, and then from the ground to the internal storage. I used Onshape to design all the custom parts and create the entire assembly.
​
The next step was to add a ramp to guide the tennis balls to the storage, but the beavertail design was failing in our tests. The pulleys was not gripping or centering the tennis balls well enough, and it was clear that this design was not going to work.
Intake V2 - Mechanum Grip
I decided to completely redsign the intake, and chose a modified verson of a mechanum grip intake mechanism. The team had used a similar design in the past that worked well and was simpler to assemble.
This design uses mechanum wheels, which have one directional angled rollers imbedded in the wheels. The rollers push the tennis balls against the robot's safety bumper to successfully grip and center them. Once centered, pulleys would carry the balls up and over the bumper. The mechanum wheels reliably centered the tennis balls every time, so I decided that using pulleys here would be effective and could drag the tennis balls along a ramp.
I also made this design in Onshape, importing parts like the motors, bearings, and mechanums while creating parts like the sideplates, ramp, spacers, and the tubing.

Intake V2 Side Plate

This intake design requred custom sideplates to support the mechanum wheel shaft, the pulley shafts, and the motors. I made this part in Onshape and used construction lines to map out the geometry to determine the best locations for all components
I made initial prototypes out of laser cut cardboard to test the geometry before manufacturing the final version. We assembled this intake design with the cardboard plates and determined that the mechanum wheels would successfully capture the tennis balls and the pulleys provided an appropriate amount of compression.
​
Once I finalized the design for this piece, I used our CNC mill to cut the final sideplates out of lexan, a material that its flexible, yet rigid. I chose to use lexan for the plates because it is durable and its flexibility provides protection against impacts.
Intake Drill Test!
Relevant Skills
Onshape
Used for custom side plate design and assembly creation
CNC Mill
Used to manufacture custom lexan plates
Lathe
Used to cut down hex shafts and spacers to exact size
Manual Mill
Used to manufacture metal brackets
3D Printing
Manufactured mecanum wheels, ramp, and pulley wheels